Cost-Effective Techniques for Packaging Machine Repair and Upgrades
Cost-Effective Techniques for Packaging Machine Repair and Upgrades
Blog Article
Reliable Ways to Troubleshoot Common Issues in Packaging Machine Operation
In the realm of production and manufacturing, guaranteeing the seamless procedure of product packaging devices is vital to keeping efficiency and meeting deadlines. However, also one of the most sophisticated machines are not immune to running into typical problems that can interfere with the entire production procedure. Managing these challenges promptly and properly is key to minimizing downtime and optimizing outcome. By carrying out an organized approach to troubleshooting and preemptive upkeep, drivers can not only address problems quickly however additionally avoid possible setbacks in the future. Allow's check out some effective strategies that can aid in quickly dealing with typical problems in product packaging maker operation.

Identifying Common Packaging Maker Problems
When fixing packaging equipment issues, it is critical to properly identify usual problems that may emerge throughout the packaging procedure. One common trouble come across in packaging equipments is incorrect sealing.
Electric troubles, such as faulty electrical wiring or power supply problems, are additionally usual culprits behind packaging maker failings. By identifying these issues early on, operators can stop downtime, reduce item waste, and make certain the smooth functioning of packaging equipment.
Carrying Out Regular Maintenance Checks
Routinely performing extensive upkeep checks is vital for ensuring the optimal efficiency and long life of packaging makers. By sticking to a structured maintenance schedule, potential problems can be identified and dealt with proactively, lessening downtime and costly fixings. When executing routine upkeep checks, it is vital to evaluate crucial elements such as belts, chains, seals, and sensors for any kind of indicators of wear or damage. Lubing and cleaning relocating components can help prevent friction-related troubles and make certain smooth procedure. Furthermore, inspecting and calibrating setups connected to temperature, rate, and stress can help keep the device's efficiency and precision.
Moreover, conducting routine evaluations of electrical connections and controls can help avoid electric breakdowns and guarantee the safety and security of the equipment drivers. Documenting maintenance activities and keeping in-depth documents of components substitutes and repair work can help in tracking the maker's efficiency with time and recognizing any repeating issues. Inevitably, an aggressive technique to routine upkeep checks is extremely important in maximizing the efficiency and reliability of packaging equipments.
Fixing Electric and Mechanical Issues
Effective troubleshooting of mechanical and electric problems in product packaging equipments calls for an organized technique and a deep understanding of the machine's elements and procedure. When dealing with electric issues, beginning by checking power sources, connections, and control panels for any noticeable damages or loosened links.
On the mechanical front, problems like jams, misalignments, or extreme vibrations can interrupt product packaging procedures. To deal with mechanical problems, perform a detailed visual examination of moving parts, belts, chains, and gears for indicators of wear or damages. Our site Lubrication of key elements can avoid friction-related issues and ensure smooth maker procedure. Moreover, verifying the next alignment of elements and readjusting stress where needed can remedy problems associated with misalignments or unequal motions in the packaging device. By combining a methodical approach with a comprehensive understanding of the equipment's operations, effective troubleshooting of mechanical and electrical problems can be attained, decreasing downtime and enhancing production result.
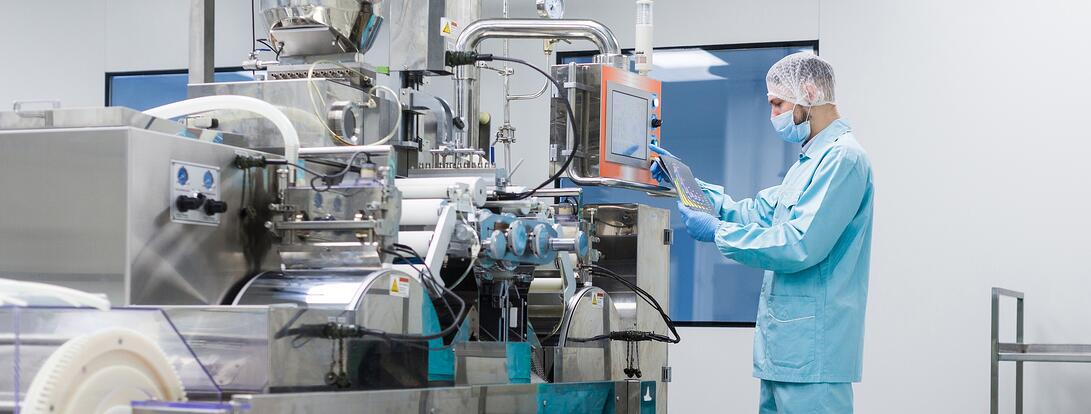
Optimizing Machine Setups for Efficiency
To boost the overall efficiency of packaging machines, a critical element involves fine-tuning and enhancing machine settings for optimal efficiency and result consistency. Properly calibrated equipment settings can dramatically affect the rate, accuracy, and high quality of the packaging process. One essential component to take into consideration is readjusting the equipment's rate settings to find the optimal balance between performance and accuracy. By fine-tuning the rate, you can avoid problems such as jams or misaligned packaging. In addition, readjusting the pressure settings, including the sealing and cutting pressures, is vital for ensuring that packages are secured firmly without harming the materials. Making sure the right temperature level setups for sealing aspects such as heat sealers or thermal transfer printers is additionally important to maintain the stability of the packaging. Regularly keeping track of and adjusting these device settings based upon the specific requirements of the product packaging products and product can lead to increased performance, minimized downtime, and enhanced overall result top quality.
Executing Preventative Maintenance Steps
Carrying out preventative maintenance steps is vital for guaranteeing the longevity and optimum efficiency of product packaging devices in commercial settings. This timetable must be adhered to faithfully by skilled maintenance personnel to guarantee that the machines run at peak performance.
In enhancement to arranged maintenance, it is vital to maintain complete records of all maintenance tasks carried out on the packaging equipments. These records can provide beneficial understandings into the machines' efficiency patterns, aid determine repeating concerns, and guide see here future upkeep efforts - packaging machine repair. Furthermore, buying training programs for device drivers and maintenance team on appropriate maintenance treatments and techniques can significantly improve the effectiveness of preventative upkeep steps. By prioritizing preventative upkeep, organizations can lengthen the life-span of their product packaging devices, lessen disturbances in manufacturing, and preserve regular item quality.

Final Thought
Finally, effective troubleshooting of usual problems in packaging machine operation involves determining problems, performing routine upkeep checks, repairing electrical and mechanical concerns, optimizing machine setups for performance, and carrying out preventative upkeep steps. By complying with these actions, operators can make certain reliable and smooth procedure of product packaging devices, lessening downtime and making best use of efficiency.
When troubleshooting product packaging device issues, it is crucial to accurately determine typical issues that may emerge during the packaging procedure.Effective troubleshooting of electrical and mechanical issues in packaging makers requires a systematic technique and a deep understanding of the maker's elements and operation.To improve the overall efficiency of packaging equipments, an essential aspect involves fine-tuning and maximizing maker settings for optimal effectiveness and result consistency.Implementing preventative upkeep procedures is essential for ensuring the durability and optimal efficiency of packaging equipments in industrial settings.In addition to arranged upkeep, it is vital to maintain thorough records of all upkeep tasks carried out on the packaging makers.
Report this page